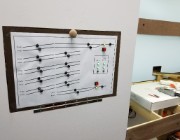
1 I have installed LED status lights for the PSX circuit breakers controlling the helix and middle level center.
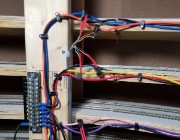
2 I wired up all 24 occupancy detection coils for the helix.
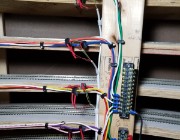
3 I wired up all 24 occupancy detection coils for the helix.
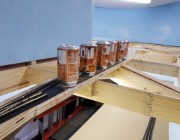
4 Gluing cork roadbed to transition from mainline to service siding.This siding will probably service a livestock facility.
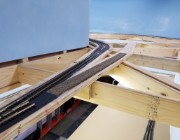
5 Cork is glued and ready to start sanding/fairing.
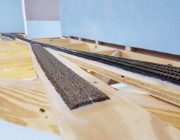
6 Need to fair the cork roadbed down to the bare plywood.
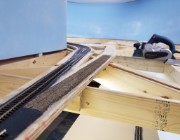
7 This time I decided to use my Bosch hand planer. Much faster than hand sanding.
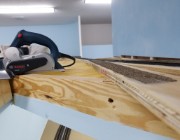
8 This time I decided to use my Bosch hand planer. Much faster than hand sanding.
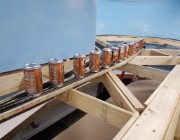
9 Gluing down the code 70 Micro Engineering flex track.
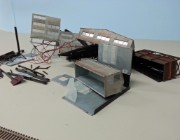
10 Jan 5 2018 - I had a bit of an accident. :( I had some the buildings/structures I built for the previous layout on a bookshelf in the model workshop. The coal mine buildings were on the top shelf. There was a framed picture sitting on the shelf behind them. I bumped the book shelf and the picture fell forward knocking the Walthers coal mine kit 7ft down onto the floor. And then the picture/frame landed on the remains of the kit.
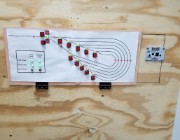
11 I moved the Digitrax UR-92 radio receiver up next to the upper level return loop control/status panel (in the center of the room).
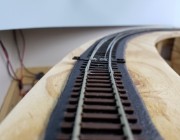
12 Noticeable kink in the track as it meets the #8 curved turnout. I need to redo this track....
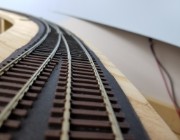
13 The exits from the curved turnout are ok.
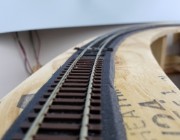
14 After redoing the track and soldering the flex track to the curved turnout. Much smoother.
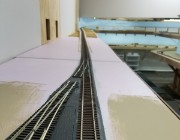
15 Starting to work on the lower helper district service track sidings.
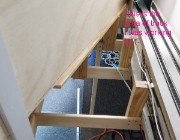
16 I had problems with the track as it passed through the backdrop and changed from code 83 to code 100 and had a double gap for occupancy detection. I redid the track so it's much more reliable.
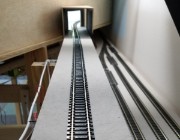
17 The new track
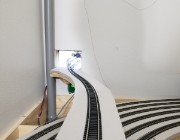
18 Headed the other way into the model workshop
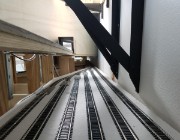
19 The view of the lower return loop and 5 staging tracks.
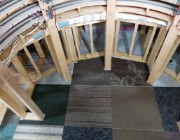
20 I laid carpet tile under the helix.
2018